Rolling with the Punches: Printing Production Spoilage
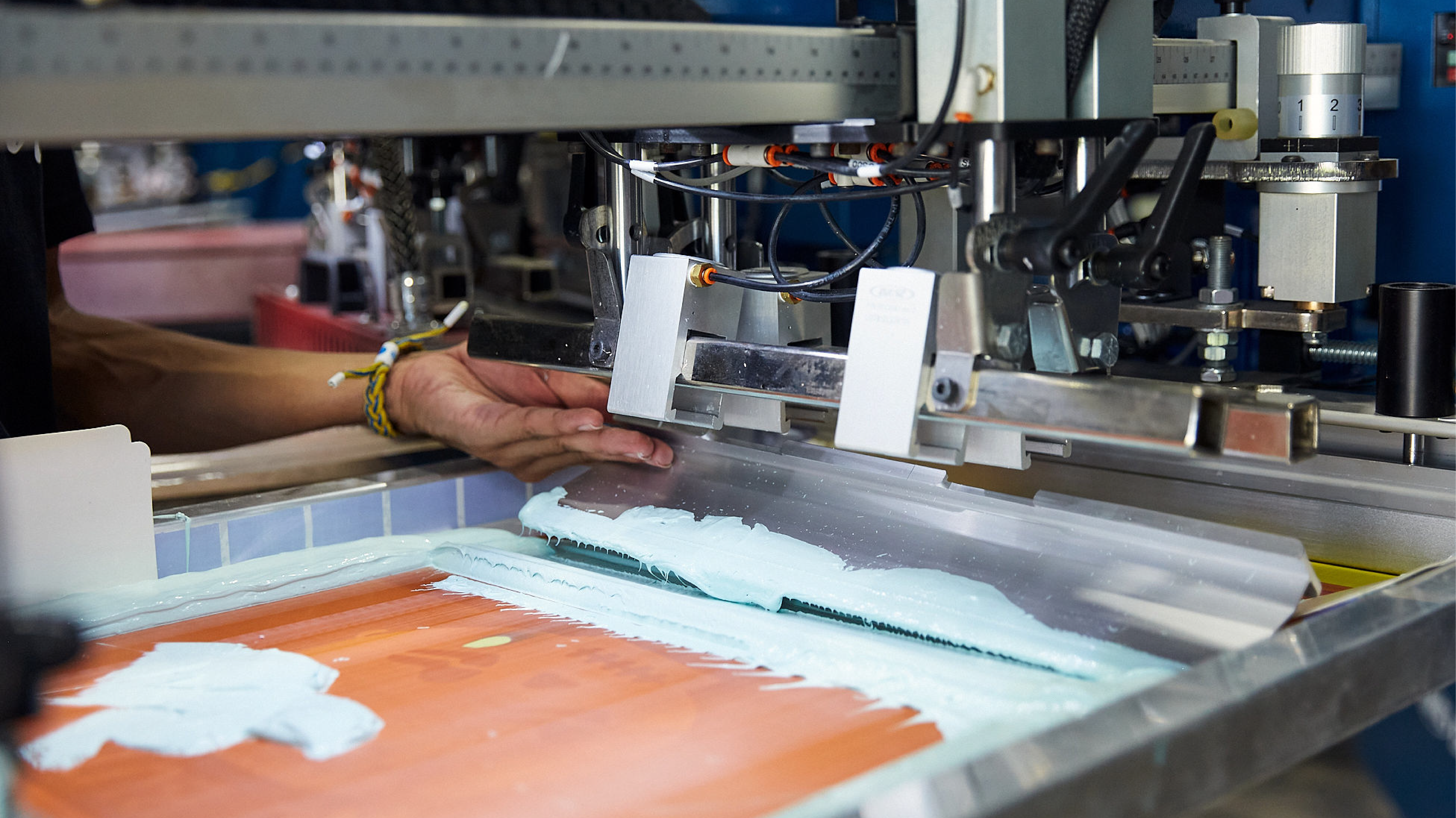
Ah, printing production—the thrilling roller coaster ride of creativity and chaos. At Threadbird, we understand that despite our best efforts, spoilage can happen when screen printing.. Whether it's a rogue ink bleed or a pesky tagging error, we want to make sure you're in a safe, and insured spot in the event that spoilage were to occur.
You may be asking, what exactly is spoilage? Let’s get into the nitty-gritty.
What is Spoilage?
Like everything, screen-printing production isn’t guaranteed perfection. Within the screen printing industry, spoilage refers to errors that can and may occur during the production process. When screen printing large orders in bulk, potential instances of spoilage such as garment pulls or tears, ink bleeds, stains or de-tagging errors can happen along the way.
In the event that spoilage was to happen to your order, this may result in what is known as an ‘under-run.’ This means that the quantity printed is under or less than the ordered quantity.
Our Threadbird team does our very best to inspect all of the garments as we print them. However, since we don’t manufacture the garments ourselves, we can’t always guarantee their perfection. There’s always the slim chance that garments may come to us from the manufacturer with some form of imperfection (loose stitching or stitching error, holes in garment, ripped seams, color inconsistency, etc).
Garment Disclaimer:
Threadbird is not responsible for manufacturer garment defects such as those listed above.
Types of Spoilage
Garment Holes i.e. Tears
Sometimes, despite our best efforts, garments can come out of the printing press with unexpected holes. This can be caused by various factors, from faulty machinery to irregular fabric quality. But fear not! Our team is well-equipped and always on the lookout to catch these types of garment flaws and remove them from the order before printing.
Ink Bleeds
Sometimes, ink reacts in unexpected ways when printed. Ink bleeds can be a dreaded nightmare for any printer. Ink bleeds are when the ink ‘bleeds’ or spreads outside of the intended print area on the garment which may result in fuzzy and blurred edges on the printed design. This can happen for a number of reasons, such as an overuse of ink, ink consistencies, or misalignment of the press. Rest assured, our team has the skills and experience to minimize and mitigate ink bleed occurrences, leaving you with crisp, clean prints that make a statement.
Stains
Stains are another common occurrence in printing production, whether it be an ink smudge or a mysterious mark that appears out of nowhere. Our expert team is trained to analyze and identify stains throughout the printing process, to ensure that any garments stains do not go unnoticed before they are printed.
Garment and Tagging Errors
From sizing mishaps to tagging mix-ups, garment, and tagging errors can throw a wrench into the production process. From time to time, printed tags can get messed up, or the shirt collar accidentally tears when we’re removing the manufacturer's tag. Or on occasion, garments will come to us from the manufacturer with a torn collar.
Details matter, and we do our very best to pay attention and catch these defects along the way. However, if you notice any of these imperfections with your order please let our team know right away! We will be happy to reprint and refund you if the spoilage has effected 10% or more of your order (10 shirts per order of 100).
Terms & Conditions
Given the unpredictable nature of screen printing, Threadbird will not be responsible for under-runs or spoilage that is less than 10% of your order (aka a minimum of 10 shirts). Threadbird will not be responsible for under-runs or spoilage up to 3% on jobs of 100 shirts per design, and up to 10% on jobs of less than 100 pieces. Please note: Spoilage must affect at least 10% (10 shirts per order of 100) in order for Threadbird to reprint or refund you for them.
Please keep this in mind when ordering (it is never a bad idea to order extras). We always do our best to get you what you ordered. We will refund you the cost of any items shorted from your order but will not process a reprint for less than 10% of your order (or 10 shirts minimum).
Threadbird will not, at any time, be responsible for any lost profits on items shorted from your order. (IE: If you paid $7.50 per shirt to get the shirt printed, but you sell them for $25.00, Threadbird is only responsible for the $7.50 you would have paid us for the shirt).
Preventative Measures (Get Ahead of the Curve)
We strive to produce and deliver your orders flawlessly, but the reality is we are human. To the best of our ability, we quality check & inspect printed garments for any spoilage. We understand that navigating the ‘what ifs’ can be tricky, but there are preventative measures that you can take for self-insurance & peace of mind.
One way to get ahead of the ‘what ifs’ is to order extra blank garments with your order. Due to the unpredictable nature of the screen printing process, ordering extra shirts gives you some cushion room in case any spoilage were to occur. If exact garment count is essential, we highly suggest ordering 5% extra of each garment size so that you can still get the intended quantity you initially ordered if spoilage were to happen.
So there you have it, folks—printing production spoilage may be an inevitable part of the journey, but with Threadbird by your side, you can rest easy knowing that we've got your back. From holes and stains to ink bleeds and tagging errors, our expert team is here to navigate these challenges with skill and finesse. So keep creating, keep dreaming, and let's roll with the punches together!